SUPPLY CHAIN MANAGEMENT
- K&R Department
- Mar 28, 2021
- 7 min read
What is supply chain management ?
Supply chain management is the process and activity of managing the flow of goods and services as well as the transformation of raw material into the final goods that the company will deliver to its customers. It also involves management of the money and information as well as end to end order fulfillment from point of origin to point of consumption. The objectives of supply chain management is to create a net value, build a competitive infrastructure, leverage worldwide logistics, synchronize supply with demand and measure the company’s performance globally which it achieves by designing, planning, execution, control, and monitoring of supply-chain activities.
Timely and effective use of accurate supply chain information allows the manufacturer to produce and ship only as much product as can be sold. Apart from this it helps manufacturer and retailer to reduce excess inventory which leads to reduction in cost of producing, shipping, insuring, and storing product that cannot be sold. It can be done by keeping tighter control of internal inventories, internal production, distribution, sales, and the inventories of company vendors.
The role of a supply chain manager in supply chain management is to coordinate the logistics of all aspects of supply chain which consist of five parts that are:
The plan or strategy
The source of raw materials or services
Manufacturing focusing on productivity and efficiency
Delivery and logistics
The return system for defective or unwanted products
Apart from performing the job about logistic a supply chain manager also give suggestions and ideas to improve the quality of the product or service as well as about the improvement in productivity and efficiency of operation.
SCM has been derived from the areas of systems engineering, industrial engineering, operation management, procurement, information technology, logistics, and marketing and it focuses on an integrated approach. The goals of supply chain management are same as supply chain engineering but supply chain management has a traditional approach focused on management and business, whereas supply chain engineering is focused upon mathematical models.
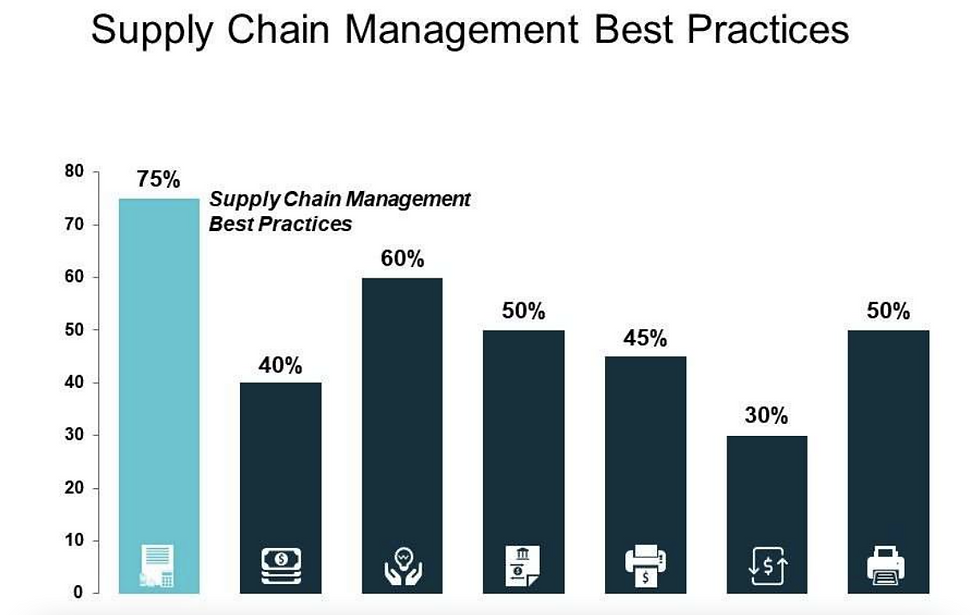
Origin of supply chain management
The first use of the term “supply chain management” is commonly related to the
Article “supply chain management: logistics catches up with strategy” by oliver
And weber (1982). They proposed to consider material flows from raw material suppliers up to end consumers within an integrated framework that has been named supply chain management.
The origins of supply chain management can also be seen in early works on postponement (alderson 1952), system dynamics and the bullwhip effect (forrester 1961), inter-firm cooperation (bowersox 1969), optimal multi-echelon inventory management (geoffrion and graves 1974), just-in-time, and lean production. The first book on supply chain management appeared in 1992 (christopher 1992).
In practice, supply chain management became important in the 1990s in retail networks, the automotive industry, electronics, and textiles. Trends of outsourcing, increased competition pressure, the establishment of new organizational forms in conditions of globalization, integration and information technology development, expanding logistic services – all of these have driven the development of supply chain management.
The practical realization of ideas of balancing and synchronizing demand and supply along the entire value-adding chain has been enabled by business information systems and the internet. Information technology provided a new level of coordination capabilities in supply chains and enabled a breakthrough in supply chain responsiveness and flexibility. Information technology, on one hand, serves as an environment to support supply chain management. On the other hand, it has been the enabler of much advancement in supply chain management. The coordination and integration made supply chains much more than simple inter organizational cooperation.
Business process integration
Business process integration (bpi) refers to the synchronization of the internal operations of a company with its other divisions and trading partners by the connection of disparate systems in real-time. It includes automation of business processes, secure sharing of data across numerous applications, and integration of system and services.
This leaves businesses free to focus on important aspects like growth and profitability, rather than being consumed in internal matters like integration. All businesses today need an efficient integration solution to streamline processes between marketing, sakes, customer service, supply chain, etc. Integration among administrative, operational, and support processes increases productivity by simplifying regular enterprise functions.
Advantages
Process gaps: BPI reduces delays or errors.
Needless duplication: Business process integration avoids duplication that wastes resources and may result in data inconsistencies.
Disparate processes: Gain a better understanding of how different processes impact each other. Essential knowledge in support of business process improvement programs.
Real-time visibility: Essential to effective business performance management programs.
Steps
1. Identification of business processes
The first step in implementing bpi is to identify processes. For this, there is nothing more appropriate than using business process mapping tools. Good bpm software, in addition to mapping, also enables process modelling and automation.
2. Process documentation
The traditional way of sharing a process is through documentation. Typically printed or pdf documents are created specifying all the details of the process, the person in charge, tasks and decision making. Some bpi tools do the documentation automatically, based on the process diagram itself, created in the tool through a drag-and-drop interface.
3. Collaborative modelling of newly integrated processes
Without the use of collaborative bpi tools, there will be a need to share the documentation, wait for the analysts at each company to study them, and set up meetings to define what the integrated processes will look like. With the use of the collaborative tool, this will be much easier. Everyone who has access to the process models can make changes and create new process diagrams from the existing ones without losing the previous ones. One can even capture one process from one organization (already modelled in the tool) “copy and paste” into another and integrate it quickly. In addition, everyone can make comments and suggestions in the processes as others model and adjust them.
4. Implementations
As the tool also automates the processes, implementation is very agile and can be accompanied by all the organizations involved. A request made by one company can trigger a process in the other that, through the same flow of tasks, triggers the suppliers in a third company, and so on.
5. Monitoring and continuous improvement
The bpi process provides for the creation of key performance indicators to track processes. Thus, together, companies and organizations can assess whether integrations are having the desired effects and provide the necessary adjustments and improvements to the processes.

Supply Chain Centroids
In supply chain management, centroids have always been a significant economic consideration. These are places that contain a high proportion of both population and manufacturing centers. In the study of supply-chain management, the concept of centroids has become a useful economic consideration. In mathematics and physics, a centroid is the arithmetic mean position of all the points in a plane figure. For supply chain management, a centroid is a location with a high proportion of a country's population and a high proportion of its manufacturing. A supply chain is the network of all the individuals, organizations, resources, activities and technology involved in the creation and sale of a product. A supply chain encompasses everything from the delivery of source materials from the supplier to the manufacturer through to its eventual delivery to the end user.
The supply chain segment involved with getting the finished product from the manufacturer to the consumer is known as the distribution channel. Because companies use the centroid method to quantify and address a key logistics question – the optimal location for a new facility -- the centroid method serves as a location decision tool.
This methodology takes into consideration the location of existing facilities, the distances between the existing facilities and the product volume shipped between them. The centroid method uses formulas to convert the location and volume numbers into two-dimensional criteria. Companies then use the criteria to compute the two dimensional point – the map location -- that meets the criteria. Calculation methodology and needs to properly use the centroid method, first identify the existing facilities which the new facility will be mapped against.
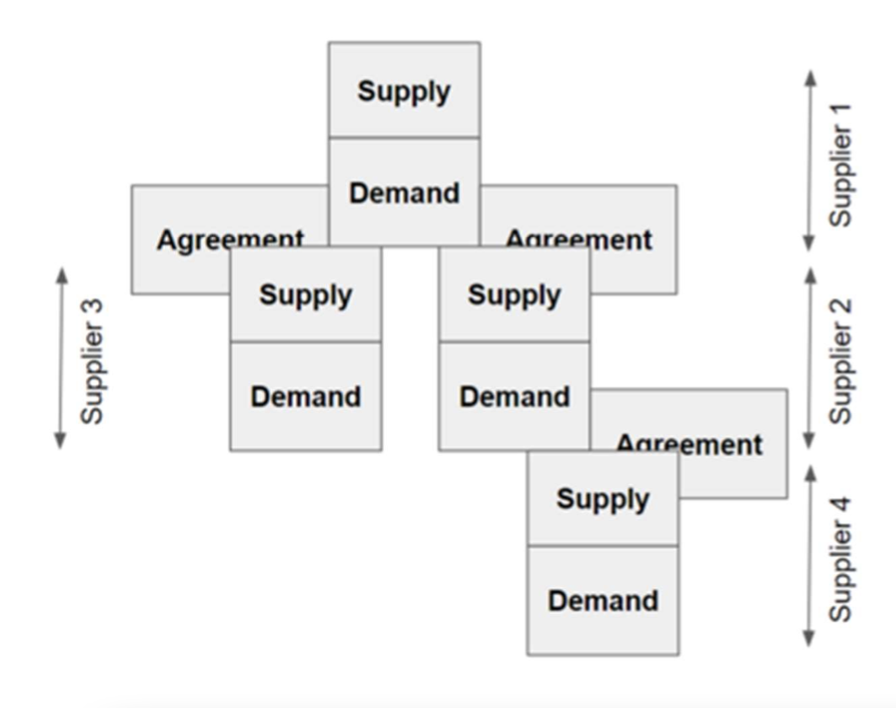
next, map these facilities on a two-dimensional grid -- for example, graph paper or an equivalent software mapping system -- to determine their coordinates. Consult with the shipping or purchasing department to obtain the volume information on the product flow at the existing facilities in the area or region. Then, calculate the new coordinates using formulas and place them on the map. Gis software, tableau and apteryx all can perform sophisticated centroid analysis that can be conducted and integrated to determine the precise location that reflects the maximization of efficiencies, minimization of costs, optimization of time savings and best location in regard to both supplier access (inbound) and market access (outbound). Other users although manufacturers and distributors often use the centroid method to locate a new distribution center or warehouse facility, many other industries use this methodology. This includes mobile service providers to locate cell phone towers; automotive dealers to locate storage facilities; and transportation companies to locate hubs.
Digitizing the supply chain is the movement towards a completely connected sequence of planning and production solutions. It relies on intelligent, integrated solutions rather than manual inputs or human intervention. The end result is a more responsive, dependable, agile, and transparent supply network that will readily adapt to a host of industry-wide unknown variables such as inventory shortages, modifications to orders, and availability of resources.
Through this integration and digital transformation, companies can experience lower cost of production and operational costs, and agile reporting and data analytics capabilities which can fuel better planning and manufacturing programs.
Key elements
Holistic integration of supply chain
It aims at bringing each important component of supply chain under the same umbrella. Companies must view planning, production, and data management solutions as part of the same overall function or plan rather than as separate function.
Connection of data sources
It aims at bring more accurate forecast of demand of the products so that mangers can make more effective planning strategies. This is achieved through iot, digitizing the supply chain connects various methods of collecting, sorting, and evaluating data.the connection of data sources also helps planners and managers create enhanced what-if scenarios and simulations, both of which are critical for driving planning schemes for production programs.
Enhanced communication
Digitizing the supply chain is a critical move toward removing communication silos across an organization. This means all the major players in the supply chain will communicate and collaborate, share information and data with greater capacity
Comments